Accurately pricing fence installations is key to winning jobs and running a successful fencing business. To help you nail those cost bid fence installations, this guide breaks down the ins and outs of estimating expenses, so you can create quotes that keep both you and your customers happy. If you’re bidding on a fencing project, here’s everything you need to know to estimate your costs.
To keep everything simple, let’s break down the task into six steps.
- Understand the Scope of the Project
- Calculate the Cost of the Materials
- Calculate Labor Costs
- Determine Overhead Expense
- Analyze Profit Margin
- Determine the Bid Price
After explaining each of these steps, we’ll also talk about how to automate the entire process using FieldBin.
Measure and Understand the Scope of the Project
Before bidding, the first step is to evaluate the total linear footage of the fence. Accurately evaluating the total linear footage of a fence is crucial for fence builders to provide precise job estimates and plan the project.
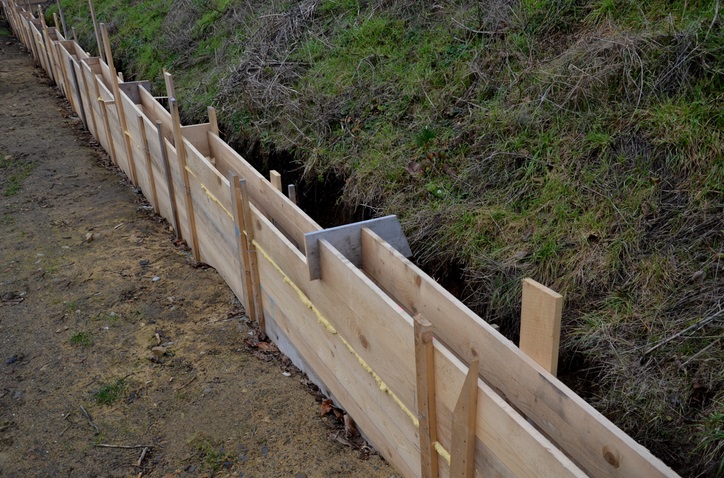
Here’s a step-by-step guide on how to calculate the total linear footage of the fence:
- Site Assessment: Begin by conducting a thorough site assessment. Walk the proposed fence line, noting the starting and ending points, corners, and any potential obstacles or land features that may impact the fence installation, such as slopes, trees, or utility lines. Proper site assessment is crucial for accurate cost estimation and project planning.
- Measuring Tools: Equip yourself with appropriate measuring tools to ensure precise measurements. A measuring wheel is ideal for longer, straight sections, while a measuring tape is suitable for shorter distances or angled sections. Laser distance measurers offer high accuracy but may be more expensive. The choice of tools depends on the specific project requirements and the contractor’s preferences.
- Measure Straight Sections: Starting at one end of the fence line, measure the length of each straight section of the fence, and record the measurements in feet. If using a measuring wheel or laser distance measurer, you can walk or point along the fence line, respectively, to obtain the measurements.
- Measure Angled Sections: If the fence line includes angled sections, measure these separately, and note down the measurements. The Pythagorean theorem (a² + b² = c²) can be used to calculate the length of the angled section (the hypotenuse) if you measure the two sides of the triangle formed by the angle. Be sure to account for any changes in direction or additional turns in the fence line.
Free Fencing Business Software
Account for Obstacles
Consider any obstacles or land features that may impact the fence building, such as trees, rocks, or slopes. If the fence needs to navigate around these obstacles, measure and include the additional linear footage required to accommodate them.
Calculate the Total Linear Footage
Add up the measurements of all straight and angled sections, including any additional linear footage needed for obstacles or land features, to determine the total linear footage of the fence.
Include Gates, Corners, and End Posts:
While measuring the fence line, identify the locations for gates, corners, and end posts. Keep track of the number of each of these elements, as they will influence material and labor costs during the fence installation.
When estimating the total linear footage, keep in mind that the following factors can also impact the overall cost estimate:
Height and Style of the Fence
The height and style of the fence can impact the overall material cost. Taller fences usually require more materials, and certain fence styles may need additional elements, such as decorative features or added supports.
Local Building Codes and Regulations
Complying with local building codes and regulations may affect your choice of materials, which can impact your overall material costs. For example, certain areas may require specific types of materials or heights for fencing, which could increase or decrease your material costs.
Land Condition
The land conditions can influence the type and quantity of materials required. Sloping land might necessitate more fence panels or customized solutions to maintain a consistent height. Different soil types may also require varying post-installation methods, which could affect the costs of concrete or gravel.
Calculate the Cost of the Materials
Fencing materials vary in price, depending on factors such as quality, style, and durability. Therefore, try to obtain fencing quotes from suppliers to accurately estimate your material costs.
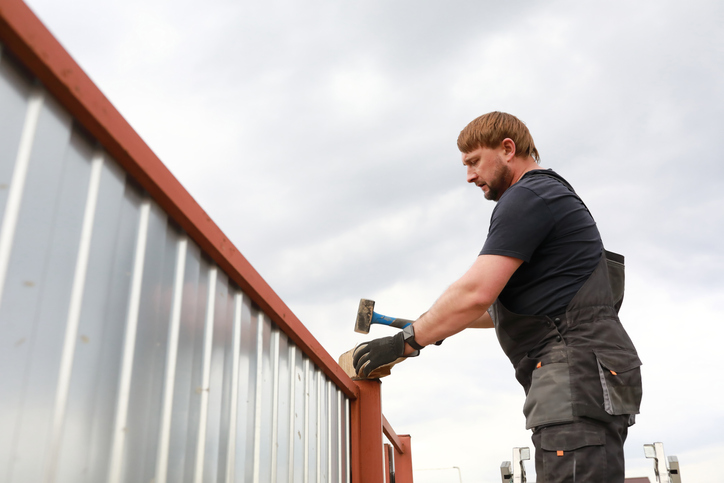
Here are some examples of average costs for various types of fencing jobs, keeping in mind that these prices are only rough estimates and can change based on specific project requirements:
Wood Fencing:
- Material cost: $7 – $15 per linear foot
- Labor cost: $10 – $20 per linear foot
- Total average cost: $17 – $35 per linear foot
Vinyl Fencing:
- Material cost: $15 – $30 per linear foot
- Labor cost: $10 – $20 per linear foot
- Total average cost: $25 – $50 per linear foot
Chain-Link Fencing:
- Material cost: $5 – $20 per linear foot (depending on the gauge and coating)
- Labor cost: $10 – $15 per linear foot
- Total average cost: $15 – $35 per linear foot
Aluminum Fencing:
- Material cost: $20 – $30 per linear foot
- Labor cost: $10 – $20 per linear foot
- Total average cost: $30 – $50 per linear foot
Wrought Iron Fencing:
- Material cost: $25 – $50 per linear foot
- Labor cost: $15 – $25 per linear foot
- Total average cost: $40 – $75 per linear foot
Composite Fencing:
- Material cost: $20 – $40 per linear foot
- Labor cost: $15 – $25 per linear foot
- Total average cost: $35 – $65 per linear foot
Additional Components and Their Cost Ranges
Apart from the fencing material, various additional components are necessary for a successful fence-building project. Following is a cost range for these essential components to help you better understand the overall expenses involved in building a fence.
Also note, this cost is already incorporated into the material costs, described above.
Concrete for Post Bases
Concrete is crucial for securing fence posts, providing stability and strength. Typically, it costs between $0.20 and $0.40 per pound.
Planks (Wood Fences Only)
For wooden fences, planks are an essential component. The cost per plank can vary, depending on the type and quality of wood, and may range from $6 to $10 per plank.
Top and Bottom Rails
Rails provide structural support and can be made of different materials, each with its own cost range:
- Wood: $8 to $12 per rail
- Wood with Metal: $40 to $50 per rail
- Vinyl: $75 to $95 per rail
- Composite: $75 to $95 per rail
Panels (Privacy Fences)
Privacy fence panels are typically priced at $225 to $325 per panel, depending on the material and design.
Posts
Fence posts come in various materials and have different costs associated:
- Wood: $3 to $5 per post
- Metal: $1 to $3 per post
- Vinyl: $75 to $95 per post
- Composite: $75 to $95 per post
- Post Caps:
Post caps add a finishing touch to fence posts while protecting them from the elements. The cost for post caps ranges from $20 to $40 per cap, depending on the material and design. - Gates:
Gates provide access and security to your fenced area. The cost for a standard gate can vary significantly based on the material, design, and size, with prices starting at $200 and going up to $600 or more for custom or larger gates
Calculate Labor Costs
Labor costs play a significant role in determining the overall expense of a fence installation project. Sometimes, building contractors include labor costs in the total cost of the material, as illustrated in the previous section.
Following is an extensive overview covering this topic:
Average Labor Cost
The average labor cost for a fence building contract typically ranges from $30 to $50 per hour, depending on factors such as the type of fence, project complexity, and the experience level of the installers. Some fencing companies may charge a flat rate per linear foot, which can range from $10 to $30, depending on the material and design.
Free Fencing Estimates Software
Factors Influencing Labor Cost
Several factors can influence labor costs in fence installation projects. These include:
- Type of Fence: Different fence materials and designs require varying levels of skill and effort. For example, installing a chain-link fence is generally less labor-intensive than installing a wrought iron or wood fence.
- Project Complexity: Complex projects, such as those involving sloping terrain, numerous turns, or custom designs, may require additional labor hours, leading to higher labor costs.
- Location: Labor costs can vary depending on the geographical location, as wages and cost of living differ from one region to another.
- Experience Level: Highly skilled and experienced installers may charge more for their services, but they can often complete the job more efficiently and with better quality.
Calculating Labor Cost
You can calculate your labor cost by:
Multiplying the estimated number of hours by the average labor cost per hour, or the total linear footage by the average labor cost per linear foot,
Let’s look at an example:
- Total linear footage of the fence: 150 feet
- Average time to install 1 linear foot of the fence: 15 minutes (or 0.25 hours)
- Number of workers: 2
- Average labor cost per hour for a worker: $40
Step 1: Calculate the total hours required for one worker to complete the project:
Total hours for one worker = (Time to install 1 linear foot) × (Total linear footage)
Total hours for one worker = 0.25 hours/foot × 150 feet = 37.5 hours
Step 2: Calculate the total hours required for all workers:
Total hours for all workers = (Total hours for one worker) × (Number of workers)
Total hours for all workers = 37.5 hours × 2 = 75 hours
Step 3: Calculate the total labor cost:
Total labor cost = (Total hours for all workers) × (Average labor cost per hour)
Total labor cost = 75 hours × $40/hour = $3,000
In this example, the total labor cost for installing a 150-foot fence with two workers charging $40 per hour would be $3,000. Keep in mind that these are hypothetical numbers, and actual costs may vary depending on factors such as project complexity, location, and workers’ experience levels.
Calculate Overhead Expense
Overhead costs are indirect expenses associated with running a fencing business, such as office rent, insurance, advertising, employee salaries, vehicle expenses, and taxes. These costs must be accounted for in a fencing professional’s bid to ensure a profitable project.
Let’s walk through a mathematical example of calculating overhead costs for a small fencing company bidding on fence jobs:
Suppose the company has the following annual overhead costs:
- Home office expenses: $1,200
- Utilities (phone, internet, etc.): $1,800
- Office supplies and equipment: $500
- Insurance: $2,000
- Advertising and marketing: $1,500
- Vehicle expenses: $3,000
- Licensing and permits: $600
- Training and certification: $800
- Taxes: $2,500
- Depreciation of tools and equipment: $1,000
- Total Annual Overhead Costs = $14,900
Now, assume the company projects to generate $75,000 in revenue from fence-building projects during the year.
Projected Annual Revenue = $75,000
Calculate the Overhead Allocation Rate:
The Overhead Allocation Rate (OHR) is calculated by dividing your total annual overhead costs by your projected annual revenue and then multiplying that result by 100.
Overhead Allocation Rate = (Total Annual Overhead Costs / Projected Annual Revenue) x 100
For instance, if a fencing company’s overhead costs are $14,900 and their projected revenue is $75,000, their OHR would be 19.87%
Overhead Allocation Rate = ($14,900 / $75,000) x 100
Overhead Allocation Rate = 19.87%
Now, let’s apply the Overhead Allocation Rate to an individual fence installation contract bid.
Assume the company is bidding for a fence installation project with the following details:
Projected labor and material costs (excluding overhead and profit margin): $4,000
Projected revenue (excluding overhead costs and profit margin): $5,000
Calculate the Allocated Overhead for the Bid:
To find the Allocated Overhead for a specific bid, you would multiply the Total Project Revenue for that bid by the Overhead Allocation Rate (OHR), after dividing the OHR by 100 to convert it to a decimal.
Allocated Overhead for a Bid = (Total Project Revenue for the Bid) x (Overhead Allocation Rate / 100)
Using the previous example’s OHR of 19.87%, a fence installation project bid of $5,000 would have an Allocated Overhead of $995.
Allocated Overhead for a Bid = ($5,000) x (19.87% / 100)
Allocated Overhead for a Bid = $995
In this example, the allocated overhead cost for the fence installation contract bid is $995. This amount should be factored into the total bid price to ensure the company covers all expenses and maintains profitability.
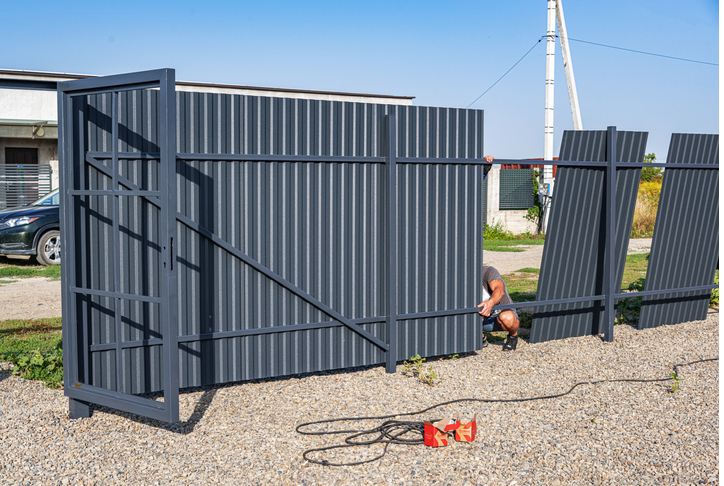
Analyze Profit Margin
After calculating the project cost, labor cost, and overhead on each project, you’re ready to calculate your profit margin.
Steps to Calculate Profit Margin for a Fencing Contract Bid
1. Calculate Direct Costs
Estimate the total direct costs associated with the fencing project, including labor, materials, and any other project-specific expenses.
2. Allocate Overhead Costs
Calculate the allocated overhead costs for the specific fencing contract bid, as previously explained in the article on calculating overhead for a fencing contract bid.
3. Determine Desired Profit Margin
Decide on the profit margin you want to achieve for the fencing project, expressed as a percentage of the total project cost (direct costs + allocated overhead).
4. Calculate Total Project Cost
Add the direct costs and allocated overhead costs to obtain the total project cost.
Total Project Cost = Direct Costs + Allocated Overhead
5. Calculate the Desired Profit Amount
Multiply the total project cost by the desired profit margin percentage to determine the desired profit amount.
Desired Profit Amount = Total Project Cost x (Desired Profit Margin / 100)
6. Determine Bid Price
Add the total project cost and the desired profit amount to calculate the bid price.
Bid Price = Total Project Cost + Desired Profit Amount
7. Calculate the Actual Profit Margin Percentage
Divide the desired profit amount by the bid price and multiply by 100 to obtain the actual profit margin percentage.
Actual Profit Margin Percentage = (Desired Profit Amount / Bid Price) x 100
Free Fencing Invoicing Software
How to Determine the Bid Price?
Based on the steps outlined in the previous section, here’s an example of how to determine the bid price:
Assumptions:
- Direct costs: $5,000
Allocated overhead costs: $1,500
Desired profit margin: 25% - Calculate the total project cost: $5,000 (direct costs) + $1,500 (allocated overhead) = $6,500
Calculate the desired profit amount: $6,500 x (25% / 100) = $1,625
Determine the bid price: $6,500 (total project cost) + $1,625 (desired profit amount) = $8,125
Calculate the actual profit margin percentage: ($1,625 / $8,125) x 100 = 20%
In this example, the bid price should be $8,125, and the actual profit margin percentage should be 20%.
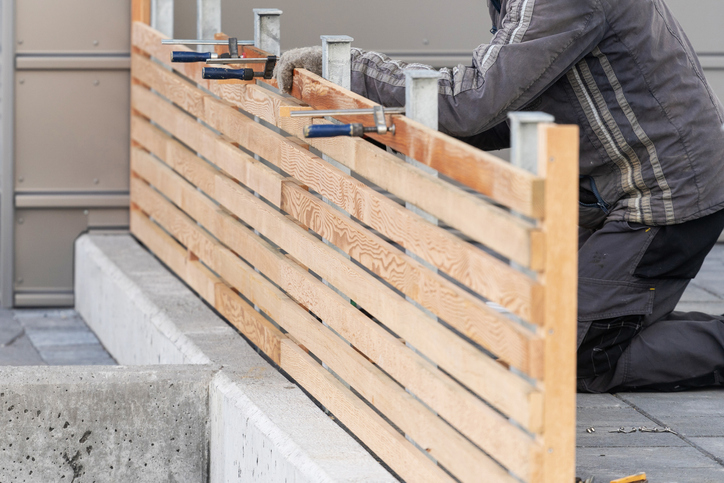
How to Automate the Entire Process
Now that you’re ready to bid, it makes sense to invest in fencing software that can automate the entire process.
Remember, bidding on a fencing job requires careful consideration and accurate calculations to ensure competitiveness and profitability. By thoroughly assessing project requirements, factoring in material, labor, and overhead costs, and applying the desired profit margin, fencing professionals can create precise and successful cost estimates.
By utilizing tools and software like FieldBin, contractors can further streamline and automate their business processes, making it easier to manage their operations efficiently. Ultimately, understanding the nuances of bidding and leveraging technology can lead to a more profitable and successful fencing business.